Aerial Apostle Animation
Aerial Apostle is a place where I can showcase my stop motion animations and provide some insight into how they are made.
Tuesday, May 14, 2019
Saturday, December 19, 2015
Sequel: Part III
I know it's been over a year, but I have been very busy, seriously. Anyway, here is the my latest project called Sequel: Part III. It's a continuation on the same themes presented in the first two Sequels.
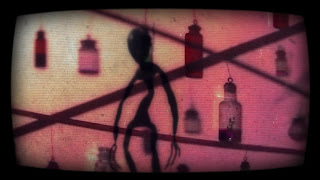
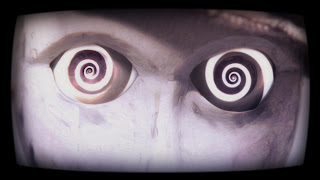
Friday, October 31, 2014
Flying Universe Helmet or Steampunk Diving Helmet
I had this dream in which the people of a town would take take turns putting on a suit and flying around the universe. The only problem was, when they returned they had grown all sorts of tumors and their bodies would fall apart when the suit was opened. I woke up in the middle and wrote down "Tumor flying universe suit/Animal characteristics chamber" on a piece of paper and went back to sleep. Unfortunately, I do not remember what animal characteristics chamber means but I did remember the suit. It was basically an an old diving suit with way too many attachments. So...
To start, I needed a wooden ball. I really wanted to get started on this project while the memory was still fresh in my mind so I decided to make one myself. I glued together 4 1x4 of pine and cut out a basic ball shape with my band saw. I then used a belt sander to smooth down the edges.
From there, I tapered one side of the ball.
Then, I sketched out where to drill the holes for the various ports and hoses etc.
Drilled the holes...
Base coat...
Metallic paint...
Then I looked a picture of an old diving helmet. I had forgot to make the neck and shoulders. So, I cut a couple of pieces out with my band saw to make the neck/shoulder piece
Two coats of paint with light sanding in between later and it totally started to look like a diving helmet.
The next step was to dent the surface of the wood to make it look like it was hammered. I took a pachinko ball and put it in the round indentation by the wire cutters on a pair of needle nose pliers. I probably should have used a ball peen hammer, but I did not have one.
I pounded, and pounded.
And more pounding.
I wanted the the pieces for the port holes and such to be made of metal so I went shopping. I spent a good hour at the hardware store picking out randoms pieces from every department to put on my helmet.
I glued random pieces together to make the port holes, and filled the other holes with whatever I could find.
Now I just need a suit.
Wednesday, October 15, 2014
"High Five Earl"
I taught my cat how to high five.
Although this has little to do with animation, I thought it was something that needed to be shared. Oh, and I did use After Effects to put it together.
Although this has little to do with animation, I thought it was something that needed to be shared. Oh, and I did use After Effects to put it together.
Thursday, September 25, 2014
Lamp
To celebrate the one year anniversary of this blog I decided to do something special. Special like lamp. My initial concept involved a working lamp with a led, but I quickly abandoned this because the led was too bright. It really messed up the lighting in my tiny apartment. So... I decided to make a non working lamp and light it in post with After Effects.
Sexy wood.
Shiny.
Sexy shiny wood.
Paint it black with Instagram.
This is literally trash that drilled holes in to put my sexy wood in. The piece on the left is left over from some super magnets. The piece on the right is from a spray bottle. I used to spray my cat with it when he was bad, but he has been especially good lately.
More trash (tagboard from the recycling and an old pillow case).
Trash glued to other trash.
More glue.
Trash + trash...
= 0
Sexy wood + trash...
= :/
Put it all together... Lamp.
Wood.
Sexy wood.
Shiny.
Sexy shiny wood.
Paint it black with Instagram.
This is literally trash that drilled holes in to put my sexy wood in. The piece on the left is left over from some super magnets. The piece on the right is from a spray bottle. I used to spray my cat with it when he was bad, but he has been especially good lately.
More trash (tagboard from the recycling and an old pillow case).
Trash glued to other trash.
More glue.
Trash + trash...
= 0
Sexy wood + trash...
= :/
Put it all together... Lamp.
Monday, September 8, 2014
Thursday, August 7, 2014
Effects Comparison
I really love before and after shots of effects in movies. It gives you a look into how the effects were accomplished.
Here are some before and after shots from my latest animation. All effects were done in After Effects.
The fade and blur really help the draw the viewers attention the the center. Especially in this scene with so much clutter in the background.
Here are some before and after shots from my latest animation. All effects were done in After Effects.
The fade and blur around the edges helps to center the focus on the character.
Just in case you wanted to know what a man riding an upside down unicorn looks like.
I didn't know what the character was drawing when I animated this piece so I had to add the unicorn in post.
This shot is composed of three completely separate animations. The thought bubble was shot on a green screen and the eyes were shot on video and cut out in photoshop.
There were guidelines draw in pencil on the paper that I removed in photoshop before animating.
Both the eyes and mouth were edited in photoshop before animating.
He is terribly sad.
In this shot, I added a faint reflection in the eyes. It was not in the original storyboards but I was using the same effect on another project and just thought it looked really good.
The fade and blur really help the draw the viewers attention the the center. Especially in this scene with so much clutter in the background.
Subscribe to:
Posts (Atom)